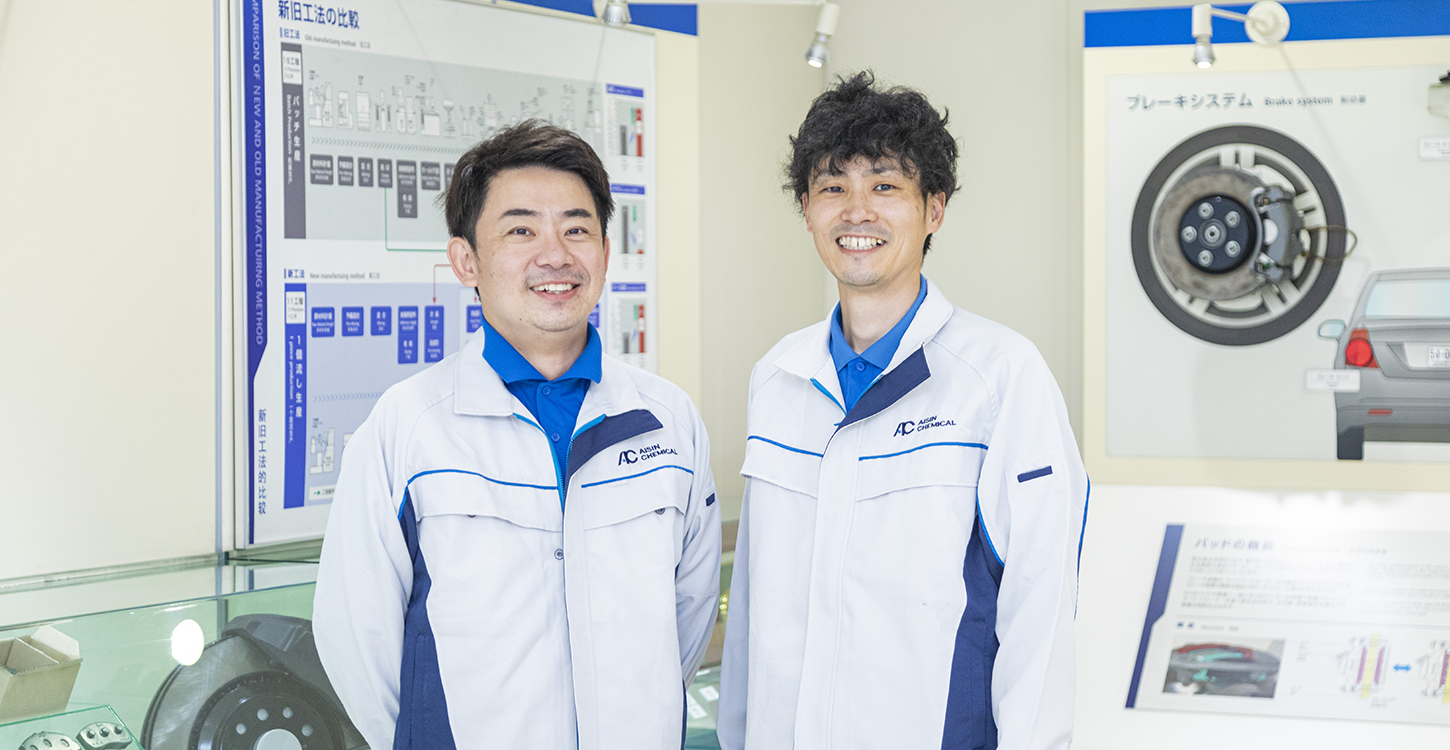
- (左)生産技術部 パッドグループ
チームリーダー 柴田 健太朗 - (右)生産技術部 パッドグループ
担当員 古橋 伸夫
既存の考え方の延長では、画期的なアイデアは生まれない。生産効率に革新を起こすには、ときに従来の基準を根底から疑うブレイクスルーが必要だ。簡単にはそれが許されない自動車部品の世界で、見事にやってのけた技術者たちの取り組みをご紹介しよう。
自動車部品は、つねに「よりよい製品を、より低コストで」実現することを求められている。100年に一度といわれる自動車業界の大変革期を迎えたいま、その必要性はますます高まっている。
アイシン化工の主力製品の一つ、ブレーキパッドを担当する生産技術部パッドグループでも、まさにその課題に取り組んでいた。いくつもの可能性を探る中で、有力と思われたのが、ブレーキパッド生産の前処理工程の一つ「接着剤塗布工程」の見直しだ。そこで2017年から、当社のお客様であり製品設計を担うブレーキメーカーと一緒に、会社の垣根を越えてプロジェクトを立ち上げ、模索が始まった。
このプロジェクトには大きな特徴があった。それは、製品の「あるべき姿」に立ち返って見直すこと。つまり、改善した工程でつくられた製品の品質を判定する際、「従来品と同じ規格の範囲内だから」という理由で合格とするのではなく、「本当にその製品に必要な品質はどのレベルか」を再検討し、新たな基準によって判断しようとしていたのだ。そう聞くと、「普通のことでは?」と思われるかもしれないが、ブレーキは人の命を乗せる自動車の重要保安部品。品質の判断には過去の積み重ねを考慮するのが、自動車業界では通常のやり方。そうではない方法を部品メーカーが提案しても、簡単に自動車メーカーの了解が得られるものではないのだ。
ブレーキパッドは、鉄の板に、摩擦材を貼り付けてつくられる。このとき接着剤を塗布して乾燥させる工程が、見直しの対象である「接着剤塗布工程」だ。テストに取り組んだのは古橋。量産用の設備を使い、良品となる乾燥の温度や時間の上限·下限を、実験で探っていく。
その一方で、それが「あるべき姿」であるかどうかを判断するための「指標」も模索する必要があった。接着剤のどの成分が、どのような数値になっていれば、乾燥したといえるのか。仮説を立ててブレーキメーカーに提案し、品質的に問題がないかの検討結果を待つ。
「別会社であるため、視点や優先順位が違い、思うようにやりとりが進まないじれったさもありました」と古橋。しかし、お互い「良くしていこう」という共通した意識の下、スタートから2年ほど経った2019年、適正な製造条件にたどり着くことができたという。その効果は、接着剤塗布工程にかかる時間を、従来の1/2に短縮。つまり生産能力を2倍にするものだった。
ブレーキパッドは、お客様であるブレーキメーカーに納入した後、直接、交換部品として自動車用品店などに販売される製品と、自動車メーカーに納入され、新車に搭載される製品がある。後者に新たな製造条件を適用するには、自動車メーカーの了承を得る必要があるが、前者はブレーキメーカーの承認があれば販売可能だ。古橋が見いだした新たな製造条件は、まずタイの市場に向けた、交換部品用ブレーキパッドの生産に適用されることとなった。
タイで量産立ち上げを行うことになったのは、量産設備の保有台数が多いため、様々なトライアルがしやすいという背景による。早速、タイの現地法人に赴任していた柴田に、日本の古橋から製造条件が伝えられた。柴田は、タイでの量産テストに向けて、半年ほどかけて国内で生産条件の確認を重ねていた。ただ、量産テストを実際に行うのはタイ現地に入ってからだったため不安もあったかと思いきや、「そこで不具合が起きるとはあまり思わなかった」と言う。
実は、もともと柴田と古橋の2人は同じ部署の1年違いの先輩·後輩で、柴田がタイに赴任してからも、定期的にコミュニケーションを取っていた。信頼関係があった上、プロジェクトの経過も共有していたため、スムーズに次の段階へ移行することができたのだ。
「逆に、現地のスタッフの驚きの方が大きくて、『本当にその条件を変えていいんですか?』と何度も聞かれました。でも、やってみたら悪影響がないとわかったので、彼らにとっては先入観にとらわれないことの大切さを学べた、貴重な仕事になりました」と柴田は笑う。
タイでの量産がスタートした後、古橋は日本国内の工場における新条件適用に向けて動いていた。特に重要だったのが、新車に搭載していただくブレーキパッドにも同じ製造条件を適用するための、自動車メーカーへの説明。ブレーキメーカーと一緒に訪問しては説明を行い、理解を得るよう努めた。
「自動車メーカーの品質担当者は長年ブレーキパッドを担当されている方で、品質に対してとても厳格。工法の変更が品質に予想外の影響を及ぼすのではないかという点を、非常に気にされていました。その場では的確な回答ができず、宿題として持ち帰ることも多々ありました」と古橋。ただ、苦労はありつつも「予想外の影響」が起きることがないことを丁寧に説明し続けることで、最終的には自動車メーカーの担当者も納得されたという。
その後、古橋はブレーキメーカーとともに、製品の納入先である複数の自動車メーカーすべての了承を得た。現在では、タイと日本、中国の工場でアイシン化工が製造を手がける全ブレーキパッドに、この製造条件が適用されている。
古橋は「使用する機械の台数を減らせた」と一定の成果に満足する一方で、「時間短縮できたのは、あくまで全7~8工程あるブレーキパッド製造工程の中の、1工程にすぎません」とも言う。それでも製造全体にかかる時間を1~2割短縮することに貢献しているが、まだゴールだとは思っていない。現に今も「あるべき姿」を目指して、新たな工法の開発に挑んでいる。
今後は「今までの製品のつくり方にとらわれず、抜本的に解決を図った今回のプロジェクトのような姿勢で、まだ人の手に頼ることの多いブレーキパッド製造工程の省人化や、デジタル技術を駆使したスマートファクトリー化に挑みたい」と柴田。
「カーボンニュートラルを含め、社会情勢が激変する中で、いかにシンプルな工程でより良いモノをつくるか。我々が独自に目指せることはいくらでもあります」。
古橋もその言葉にうなずく。「ブレーキパッドは、今のような製品になってからあまり変わっていません。それだけ変えるためのハードルが高いからです。でも、変える余地はある。生産技術にとって、変革を求められる今の時期は、まさに一大チャンスだと思います」。